
MBDA Germany’s (MBDA-D) missile propulsion manufacturer, Bayern-Chemie, has returned to Raytheon’s industrial supplier base for the Patriot missile defence system this year.
By the time that demand for Patriot missiles diminished at the close of the Cold War, the Bavarian company had produced over 2,300 rocket motors for PAC-2 missiles from 1987 to 1996; this makes the lifetime of its PAC-2 rocket engine nearly 40-years-old.
Now, the provider is ramping up production once again for the next-generation PAC-2 variant: the Patriot Guidance Enhanced Missile (GEM-T) interceptors.
This new build is equipped with a track-via-missile guidance system. Midcourse correction commands are transmitted to the guidance system from the mobile engagement control centre.
Carrying a high-explosive 90kg warhead, the missile has a range of 70km and a maximum altitude greater than 24km. The minimum flight time is less than nine seconds while the maximum is three and a half minutes.
Supplying the Bundeswehr and Nato partners
As tensions continue to simmer in Eastern Europe due to Russia’s full-scale invasion of Ukraine, several European countries have donated their missile defence systems to the war-torn country, which has depleted their inventories in recent months.
The Bundeswehr is among those re-stocking, which Thomas Gottschild, Managing Director of MBDA-D, commented at an international press event in late October at its Schrobenhausen site, that the company is focused on “filling the gaps in the Bundeswehr, not so much on new capabilities.”
As a result, there has been an increase in missile procurements across Europe to restore the stockpiles to optimum levels to meet their national security requirements. It is no surprise that GlobalData intelligence projects Europe to be the leading geographic segment in the global missile defence market, accruing a 31.1% revenue share.
MBDA-D plan to ramp up production of its vast portfolio, including the Patriot missile components it is responsible for, Enforcer, Taurus, Brimstone, Meteor and Arrow3 missiles, among others.
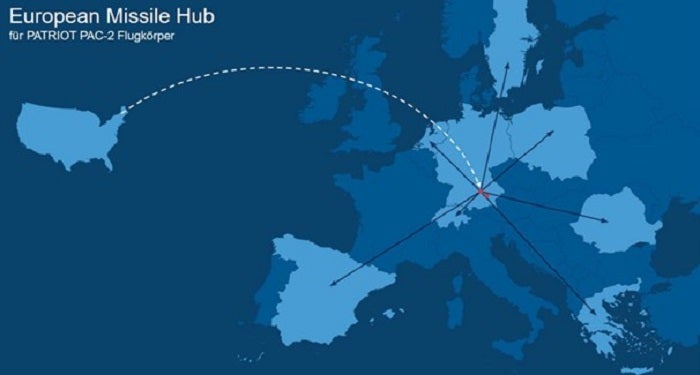
When it comes to its Patriot commitments, head of sales and business development at MBDA-D, Michael Rieder, observed “we have a lot of infrastructure here [in Bavaria] for it.”
Rieder also noted the use of PAC-2 and PAC-3 throughout the next decade. We can expect the dual use of both versions for the next ten years, until PAC-2 is discontinued in 2032.
According to GlobalData Defence Analyst, Wilson Jones, “PAC-2’s are larger, have a bigger warhead, and can travel longer and higher distances. PAC-3’s are smaller, carry a smaller warhead, and have reduced ranges, but the trade off is that they can move faster and are more manoeverable.”
Wilson continued to explain the market attraction of both versions.
“Because the PAC-3 is much more accurate, it is designed to smash into its target, while the PAC-2 just needs to get close enough for the target to be in the blast. The PAC-3 is probably getting more because it is the latest system, while the first PAC-2 came out in the 1980s. This is part of why one PAC-2 is about half the cost of one PAC-3.
“Ultimately, PAC-2 and PAC-3 function slightly differently to do the same job of intercepting missiles, and are most effective when used together.”
Bayern-Chemie upscales propellent production, indicating MBDA-D’s continental ambitions
During the press event, in Aschau am Inn, Bayern-Chemie discussed their production process and their contribution to their parent company’s ambitions for an MBDA-led continental “missile hub.”
The company makes and upscales solid-fuel rocket propellants for MBDA-D’s missile portfolio, particularly Meteor, for which it is the sole-source provider.
According to Bayern-Chemie, their mixing facility produces 40 batches of propellent a year, or two tonnes per week, with an option to upscale capacity to three shifts as customer demand grows.
Meanwhile, the subsidiary’s chemical laboratory technical specialists also experiment and explore new propellants while meeting its growing production. This could take between eight to ten years to come up with a new propellant, while they modify existing propellants.
This research and development process begins with 2kg of propellant, which will increase between 10 and 30kg maximum.
It is worth noting that the chemical producer is driven by customer requirements, adapting their recipes to such qualities as a smokeless take-off, thereby reducing the rocket motor’s signature.