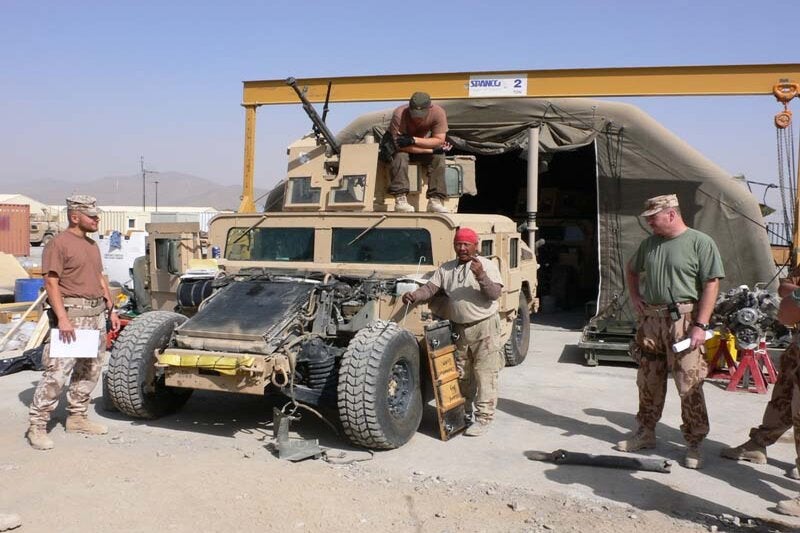
Shift5, a company founded by officers who played a crucial role in establishing the US Army Cyber Command, unveiled its latest innovation, the Predictive Maintenance Module (PMM), on 11 July
This PMM performs passive, full-take data capture from any onboard sources, and analyses the data in real time to predict and schedule maintenance.
To ensure the safety and optimal performance of defence assets, military services have been adopted policies of proactive approach to maintenance, monitoring ware and conducting interventions before failure.
The hardware-, bus-, and protocol-agnostic MPP is designed to give operators and maintainers the data-driven insights required to predict and schedule maintenance effectively.
The slow road to predictive maintenance adoption
While prioritising preventive measures is intended to improve fleet readiness, implementation of these policies has been shown to be lacking.
The US Government Accountability Office (GAO) found in a report published in December 2012 that while the Department of Defence (DoD) had issued a policy for predictive maintenance in 2002, the military services had made “limited progress” in implementing the approach until recently.
The GAO found that “the military services have not consistently adopted and tracked implementation of predictive maintenance”
While pilot programmes have been initiated, the report states that the US military does not routinely replace parts or components based on predictive maintenance forecasts. The military services have just begun “efforts to allow units to order parts ahead of need rather than waiting for the part to break”.
“[The military services have just begun] efforts to allow units to order parts ahead of need rather than waiting for the part to break”.US Government Accountability Office
In private industry predictive maintenance, personnel use condition-monitoring technologies and data analytics to plan maintenance based on evidence of necessity. This is in contrast to preventative maintenance, a type of proactive maintenance in which service personnel use periodic measurements, such as operation time or calendar time, as the basis for maintenance actions.
Where predictive maintenance has been implemented, it has assisted the military in improving maintenance outcomes. US service officials told the GAO that the routine helped reduce unscheduled maintenance, which is frequently associated with negative effects on both costs and operations.