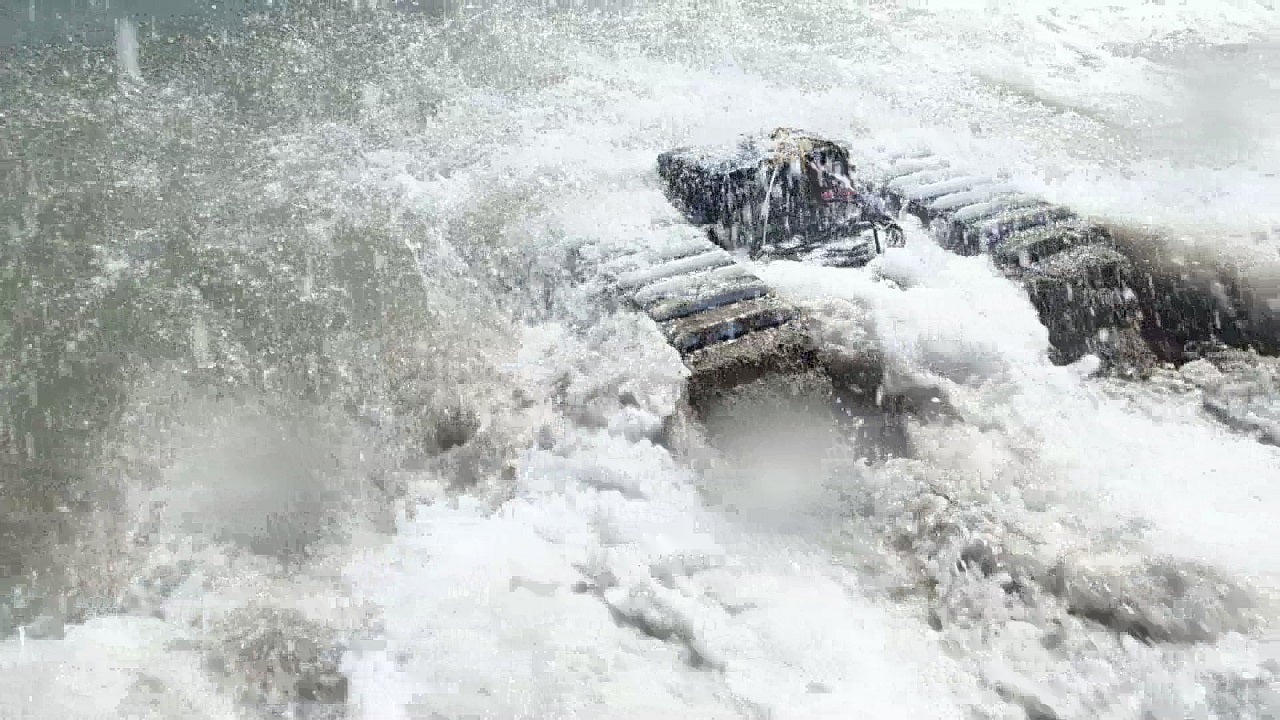
The Sea Otter littoral crawler is an amphibious, light, portable vehicle designed to transit water crossings to gather near real-time data for surveys and environmental monitoring. It is developed jointly by US-based amphibious and autonomous systems provider C2i-Engineering and UK-based marine robotics company Wight Ocean to meet the requirement for small boat deployment with smaller payloads.
The Sea Otter littoral crawler is proposed as a solution to help the British Army cross water obstacles and map the wet gaps without putting military personnel at risk.
Sea Otter littoral crawler development details
The Defence and Security Accelerator (DASA) of the UK Ministry of Defence (MoD) announced five contenders, including Wight Ocean for the Map the Gap challenge in August 2020.
The companies were awarded contracts worth £1.2m ($1.4m) for the first phase of the competition to develop semi-autonomous reconnaissance and survey systems for safe water crossing of troops. Wight Ocean was contracted to develop an amphibious bottom crawler to cross water and collect near real-time data for analysis.
The company completed the system testing phase of the Sea Otter under the Map the Gap challenge at Duxbury, Massachusetts, US, in November 2020. The uncrewed system was tested in a more than 600m-wide and 5m-deep water stretch. The phase one challenges were completed in April 2021.
Sea Otter littoral crawler technical specifications and features
The Sea Otter littoral crawler weighs 70lb (31.75kg) and has a footprint of 0.23m². It has a length of 33in (0.8m), width of 20in (0.5m), and height of 10in (0.25m). The vehicle has an open deck space that is 24in (0.6m) long and 6in (0.15m) wide.
The amphibious platform is designed to operate both on land and at sea up to a depth of 300m. The low profile and high stability of the crawler enable it to penetrate a surf zone with a wave height of up to 6ft (1.8m). A towed sled can be fitted on the crawler to carry additional sensors and payload packages.
The vehicle provides the flexibility to operate without any sea state constraints. It can function in a range of environments including rivers, dunes, surf zones, tailing ponds, marshes, and mudflats. It can be controlled by a single operator. The control modes include autonomous, tethered, and radio frequency (RF) link buoy.
Sensors and communication systems
The crawler can be integrated with oceanographic, hydrographic, environmental, benthic, and other custom sensors.
Commonly integrated sensors include global positioning system (GPS), attitude and heading reference system (AHRS), acoustic Doppler current profiler (ADCP), conductivity temperature depth (CTD), penetrometers, vibracores, single-axis fibre optic gyroscope (FOG), water level meters, video, dissolved oxygen sensors, water sample collection systems, optical turbidity sensors, and magnetometers.
The internal sensors on the Sea Otter littoral crawler help to monitor the temperature, overvoltage, and wet/dry levels of the battery. The multibeam and sidescan payloads with an integrated sensor reduce the sound velocity (SV) errors. The inclinometer, which is used for depth determination, eliminates large wave motion from the dataset. It produces a continuous dataset across the wet and dry parts. A sink gauge is fitted to avoid uncertainty related to altitude or speed over the ground.
Global navigation satellite system (GNSS) and high-precision inclinometer are used for establishing a seamless datalink from the waters to the shore in autonomous and tethered modes of control. Single or dual GNSS helps in precise positioning in waters and movements in dry environments. The precise positioning can be augmented by the use of real-time kinetic (RTK) positioning. The positional data, when combined with the inertial navigation system (INS), provides precise navigation for the vehicle when submerged in autonomous and tethered modes.
The external communication systems of the littoral crawler include ethernet tethering with 2.4GHz XBee radio frequency (RF) module. The amphibious platform can be equipped with additional optional communication equipment, including RTK and a multi-input multi-output (MIMO) RF link buoy.
The Sea Otter littoral crawler can be equipped with the Greenseas OPENSEA software, which helps in navigating wet gap crossings and measuring soil strength using the penetrometer. It is also installed with diagnostics and mission planner software from C-2i.
Mission capabilities of Sea Otter Littoral Crawler
The Sea Otter can be deployed in support of a range of missions including mine detection and clearance, hull and wharf inspections, chokepoint transit clearance, intelligence collection, and pre-positioned supply dumps from over-the-horizon (OTH) radar and synthetic aperture radar (SAR). It can also be used for environmental assessment as well as survey of beach lanes and minefields.
The system can collect bathymetric data, seafloor, water column measurements, and environmental data.
Propulsion and performance
The Sea Otter littoral crawler is powered by 54V lithium-ion batteries having a nominal output of 48.1V each. The rated power is 80Ahr with two power packs present inside the tracks. The recharge rate is four hours per battery.
The vehicle has an operational range of 16.08km in submerged traversing and 35.4km in dry conditions when operating at an average speed of 1.5kt (0.7m/s).