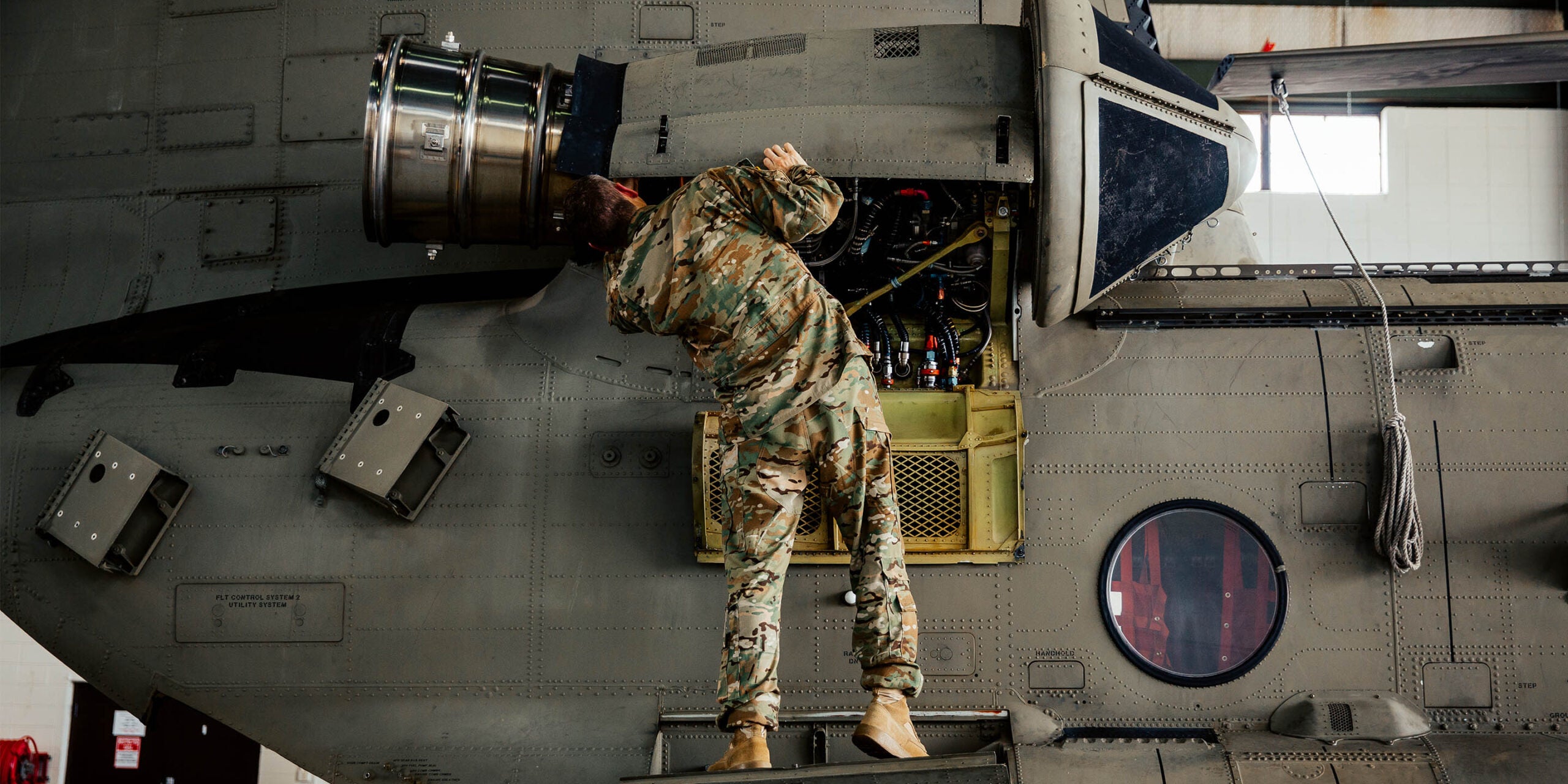
For an aircraft dating back to 1961, the Chinook has quite the fanbase among the public and armed forces alike. While the US Army is its biggest operator, contracts continue to roll in from around the world. In May the UK Royal Air Force confirmed it would acquire 14 Block II Chinooks worth £1.4bn ($2bn) through a US Department of Defence Foreign Military Sales contract, with deliveries due to start in 2026.
Despite its success, Honeywell believes it can make the Chinook even better by improving its T55 engine, a task the company is undertaking and funding independently of any customer requirement, confident it will find a market.
T.J. Pope is senior director, military turboshaft engines at Honeywell and also has responsibility for the Abrams tank engine AGT 1500 and serves as the president of Honeywell’s joint venture with advanced turbine engine company Pratt and Whitney. He explains that the Chinook has had variants of the T55 engine for the entirety of its existence.
“We’ve made multiple upgrades during that 60 year period,” Pope says. “This is a continuation of that in recognising that the operators need additional capability from a power, range and increased maintainability standpoint. Those are the key drivers for our decision to invest Honeywell dollars to make this upgrade. This is this is not a government-funded opportunity.”
High heat, heavy performance
For the last two decades the military focus for the US and many of its allies has been mainly on what it dubs the global war on terror. A lot of the demands on the Chinook have taken place in very austere environments; at very high altitudes and in hot temperatures, neither of which is conducive to optimal engine performance.
Pope says that this has driven Honeywell to seek to balance this ‘high heat and heavy performance’ in theatres such as Afghanistan with what may be next for all operators in terms of conflicts or natural disasters. The company is also looking to optimise the Chinook’s performance by increasing power and fuel efficiency and making design changes that enable more efficient maintenance. One of these is introducing digitalisation including conditioning monitoring and maintenance scheduling.
“The US Army is moving to a more commercial aircraft type of condition-based maintenance,” says Pope. “Typically, military customers tend to have inspection windows based around multiples of 40 hour intervals. The maintainers are removing things that aren’t broken just because it says on their checklist to remove them. The US Army has realised that this is not necessarily the most efficient way to conduct maintenance and are now coming to the realisation that condition-based maintenance is the future.”
The US Army programme management office dictates maintenance practices not only for the US but also all foreign military sales customers, and Honeywell is enabling condition-based maintenance and preventative and prognostic maintenance capabilities through some of its other products. These allow for safe and incorruptible data collection, and data analytics, that will give that will provide real-time data to a user via a laptop, iPad or smartphone.
Reliability and fuel efficiency
Pope highlights improved fuel efficiency as one of the most important improvements.
“We’ve increased what the operators and their aircraft can do,” he says, “the types of missions they can do, how much they can carry, where they can go.
“The other benefit of fuel efficiency is that it decreases the logistics requirements. One of the biggest budget line items for the US Army is fuel sustainment. The reason why it’s so expensive is not the gas itself, it’s the logistics behind getting it to where it needs to go. Any time we can help the operators reduce that logistics requirement, it’s a significant saving for them.”
Honeywell estimates its upgrades will deliver a 25% reliability improvement, which in turn will decrease the logistics requirement, saving dollars and time.
“The key driver for us is that our compressor is going to last 40% longer, and we’ve also reduced the part count by 27% over the existing to T55,” explains Pope. “We’re making the engine more capable and less complex at the same time. That’s enabled by driving improvements in technology, selecting different materials, and also replacing some of the LRUs [line replaceable units] with alternate designs that allow for: one, increased reliability so it lasts longer, and two, increase maintainability, so when it eventually does have to be changed, it can be changed more easily.”
Pope offers an example; on the number two side – the right side as you’re looking at the rear of the aircraft – the hydro-mechanical assembly (HMA) that manages fuel flow is positioned so maintainers have to remove the entire engine in order to work on the fuel control. Honeywell has changed the design of the T55-714C making it a top-mounted HMA so maintainers can now work on it without having to touch the rest of the engine.
“That alone will save 28% in terms of person-hours in that maintenance action alone, and also damage and rework,” he says. “Ultimately, when you have 19 and 20-year-old young men and women doing these repairs and removing this engine unnecessarily they’re more than likely going to break something else too. We like to say in the army that 50% of our maintenance is caused by 50% of our maintenance; we break this as much as we fix. Enabling soldiers to make these relatively benign repairs without putting them in danger of breaking other things is very beneficial.”
Pope says that on a standard day, defined as at sea level and 70° F (21° C), the T55-714C delivers roughly a 22% increase in shaft horsepower and an 8% decrease in fuel consumption compared with the T-55-714A. This translates to extending the circular range by 55 nautical miles, or out and back to 120 nautical miles with a 14,000 lb (6,350 kg) payload.
“We can achieve this upgrade in a substantially less expensive manner than our competitors because we are maintaining the footprint of the existing engine, so we don’t have to have to change the structure of the aircraft in order to fit our engine,” says Pope.
Another factor Honeywell says drives down the cost of integrating the engine compared with competitors’ engines is that it is available as a kit overhaul. When a 714A engine comes for an overhaul, the operator can choose to have the 714C upgrade applied as part of that overhaul action with no additional downtime.
“We’re also providing anti-ice capability on this engine,” adds Pope. My military experience was predominantly in the UH60 Black Hawk community, so I was baffled when I took this job with Honeywell and found out that the Chinook did not have anti-icing and de-icing.”
Centre of excellence
The upgrades will take place at Honeywell’s new repair and overhaul (R&O) centre of excellence in Phoenix, Arizona, co-located with the company’s production facility. It replaces an R&O facility in Greer, South Carolina.
“In addition to a smaller capacity in Greer, when you would have the one-off issues, we need to develop a unique repair in order to return that asset to the customer,” explains Pope. “Our engineers, production facilities and the ability to machine a unique partner solution are also in Phoenix, and so it made sense to relocate our R&O facility there.
“Our capacity is 20 engines per month, and we are hoping to get through 23 by the end of this month. It allows us to allocate our workforce more effectively; one of the reasons we’re striving for such a high number this month is that we cleared all of our production orders so we’re not making any new engines this month. All of the people that are normally building new engines can go work in the R&O facility. We also just take the repair engines to the production facility down the street and have extra space of capacity.”
Honeywell is currently pursuing a research and development agreement with the US Army to jointly do fit checks, ground testing flight testing on the Chinook. There is currently no US Army engine upgrade programme and Congress has not allocated budget to upgrade the Chinook engine.
“However, we’ve gotten some indications that this is something that certainly needs to happen in the future at some point,” says Pope. “Right now, we’re targeting 2024, but of course the customer will drive that decision ultimately.”