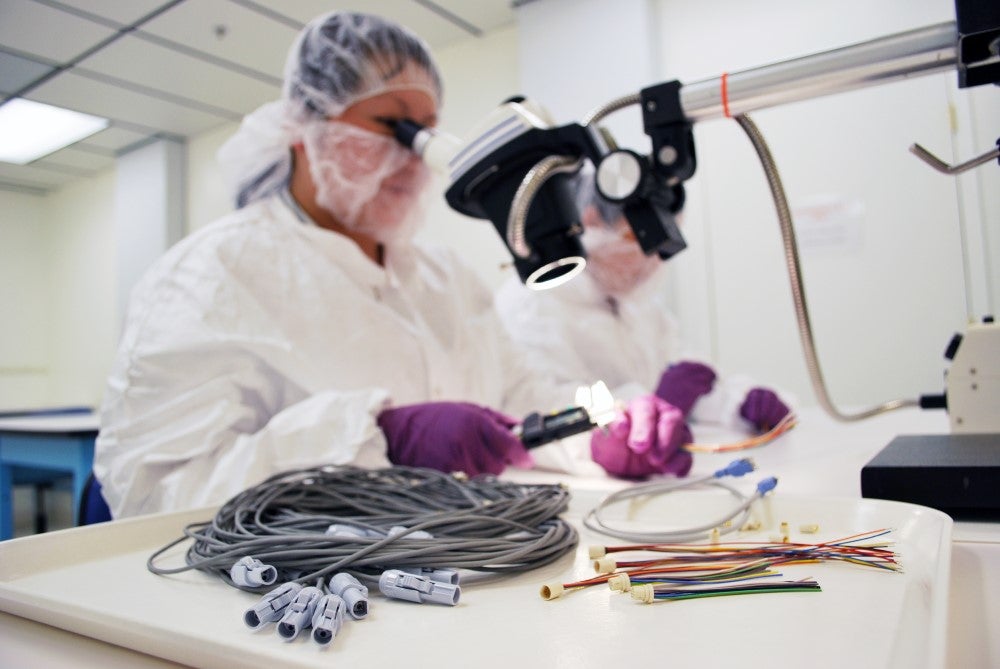
For military applications, body-worn equipment must be able to withstand severe conditions to provide soldiers with invaluable real-time data when and where it matters. Ruggedised miniature connectors and cabling can perform in the most demanding environments while offering greater flexibility, discretion, and safety than ever before.
Future soldier systems
Future soldier systems can be as simple as cabling systems that can be woven into a uniform. Lightweight electronics and flexible cabling allow for normal movement while maintaining real-time data transfer. The transfer of data such as GPS coordinates is vital for soldiers operating in military environments.
Power distribution hubs enable soldiers to carry a single battery to power all their devices, rather than needing multiple backbreaking batteries. “With a power distribution hub, you have a single cable that’s going to the battery,” says Derek Hunt, North American sales director at Omnetics Connector Corporation. “The unit itself is distributing the power to each of the soldier’s electronic devices, even where each one requires different amperages and/or voltages.”
Thinking smaller
These military applications need connector and cabling solutions that won’t weigh a soldier down and will reduce visible shiny electronics on uniforms. Ever since the integrated circuit was developed in the 1950s, cables and connectors have become smaller and lighter.
“Being able to transfer the data and the power with a much smaller form factor allows a soldier to carry less weight, while still allowing the same data transmission rates,” explains Hunt. “Usually, with the smaller connectors, you’re able to improve some of the characteristics, such as ruggedness, as well as, in most cases, data rates.”
While commercial electronics with USB connections are readily available, they aren’t typically built for battlefield environments. Military specifications (MilSpecs) require electronic devices and their connectors to handle shock, vibration, temperature changes and prevent contaminant ingress.
“We can take that commercial technology in theory of what the data transmission requirements and wants are, and we can condense that all down into much more reliable interconnect solution,” says Hunt. “You can have the same data rates in a much smaller, much more ruggedised form factor that’s been proven to perform reliably against military or aeronautical specifications and testing requirements.”
The solution is choosing the right equipment, Hunt explains: “If you’re not utilising specific connectors, you might have to separately connect your interfaces for proper power and signal distribution”. Hybrid connectors enable power and signal to be delivered by a single connector configuration, saving size and weight by replacing two connectors with one.
The challenges
The smaller connectors become, the higher the chance of crosstalk and electromagnetic interference (EMI) issues, which can cause significant problems in extreme environments. Connector suppliers must rise to the challenge of maintaining electrical signal performance, even as cabling and connectors are miniaturised. At Omnetics, signal integrity engineers design components with these demands in mind.
“We build all of our connectors families around MilSpecs,” says Hunt. “Being able to do testing to highlight performance on the back end of some of our secondary products really helps us usher new products to the market.”
By putting engineers at the forefront of the development progress, Omnetics ensures the best performance for the end user’s requirements.
“We can also help the end user by better understanding the environment that they are in, because the environment might dictate how we present a different type of cable, whether it’s a different level of flexibility or higher temperature cycling,” says Hunt. “We really embrace and double down on our customer service and really ensure that we give our customers the best solution that we can.”