
The US Army Research, Development and Engineering Command’s (RDECOM) Armament Research, Development and Engineering Center (ARDEC) is working on a project to identify, evaluate and implement an improved coating process for howitzer breech spindles.
Working in collaboration with the Product Manager Towed Artillery Systems (PM TAS), the ARDEC has shortlisted three new coating and application processes for further testing based on performance and cost. It had been evaluating 12 material formulations in small samples.
The selected processes include high power impulse magnetron sputtering from Sheffield Hallam University, accelerated plasma arc from Phygen Coatings, and electroless nickel plating.
The team had developed a list of ten primary metrics necessary for a new coating and application process, which included resistance to corrosion, mechanical wear and high temperatures.
In an effort to ensure that the coatings withstand the rigours of soldier use, the team has joined forces with the Aberdeen test center for live-fire testing on a howitzer range.
After the first round of firing, the spindle undergoes 30 days of weathering in a caustic and acidic propellant byproduct, called a swab water. This is to replicate potential combat conditions, and is followed by another round of firing and then a final weathering cycle.
How well do you really know your competitors?
Access the most comprehensive Company Profiles on the market, powered by GlobalData. Save hours of research. Gain competitive edge.
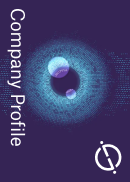
Thank you!
Your download email will arrive shortly
Not ready to buy yet? Download a free sample
We are confident about the unique quality of our Company Profiles. However, we want you to make the most beneficial decision for your business, so we offer a free sample that you can download by submitting the below form
By GlobalDataARDEC project technical lead and materials engineer Dr Christopher Mulligan said the new processes are vastly outperforming the legacy chrome electroplating in terms of corrosion and wear.
The team has also identified and funded a newly developed chemical vapour deposition type coating known as Carbonyl from Canada, and is planning to start testing over the next few months.
A final decision is expected to be made within 90 days of the completion of testing of all processes, with an aim for a production-ready coating within six months to a year.
The new technique will boost the howitzer performance, reduce the logistical burden on the soldier, and reduce environmental hazards. According to Mulligan, it will save the government more than $2m each year.
The evaluation of foreign processes and materials is being funded through the foreign comparative testing (FCT) programme.
Image: An M776 howitzer’s corroded chrome-plated standard obturator spindle sits next to a newly plated production at the US Army Aberdeen test center in Maryland, US. Photo: courtesy of Conrad Johnson, RDECOM.