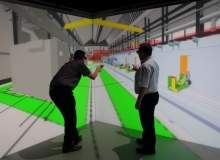
It might not have the glamour of Monaco or the adrenaline-inducing speeds of Silverstone, but building the next generation of warships can have more in common with Formula One than you probably realise. Just like a big defence project, the teams of Red Bull and McLaren have an army of designers, engineers and mechanics working away to make sure their end product is top class while also meeting strict deadlines and cost pressures.
The nature of F1 – which comprises 19 races over a nine month period – and the yearly changes to the rules which stipulate vehicle design, often requires teams to build a completely new car each season. Teams don’t have time to build prototypes or test different designs over years; cars have to be built, and perform, in a matter of months. To design, test and develop numerous designs in such a short time, Formula 1 teams have to use powerful 3D simulation software.
Now, defence and aerospace manufacturers are following suit and also increasing their use of these powerful applications – known in the industry as project lifecycle management (PLM) software – in order to bring down costs and deliver on schedule. While F1 teams are driven by the prospect of having their driver at the top of the podium, defence companies are looking to provide the best equipment, at the cheapest price, for those on the front line.
Another level – computer aided design in the 21st century
Computer aided design (CAD) has been used in manufacturing for a number of years but advances in computer technology are taking CAD to a whole new level. No longer do designers and engineers have to sit in front of a 17-inch monitor and squint at their work, new technology like virtual reality headsets means they can ‘step inside’ their design even before it’s built. Improved graphics, just like gaming and movies, is also giving engineers a much more immersive experience.
Advanced design software means ships can be tested, modified and put through the rigours of operations without ever being built. Flaws can be found and rectified early on in the design process before the first piece of metal is cut, which can save thousands, even millions, of pounds. If that same fault was found as the ship was being put together and long lead items had already been ordered and paid for, it would have severe repercussions for both customer and company.
How well do you really know your competitors?
Access the most comprehensive Company Profiles on the market, powered by GlobalData. Save hours of research. Gain competitive edge.
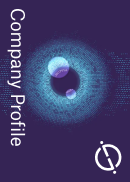
Thank you!
Your download email will arrive shortly
Not ready to buy yet? Download a free sample
We are confident about the unique quality of our Company Profiles. However, we want you to make the most beneficial decision for your business, so we offer a free sample that you can download by submitting the below form
By GlobalDataIt’s now a high priority for leading companies to integrate advanced design technology into programmes as early as possible.
British troops are set to receive over 500 next-generation armoured vehicles as part of a £3.5 billion contract.
In the design of the Global Combat Ship, also known as the Type 26, BAE Systems has invested in 3D visualisation tools for designers and engineers in its Glasgow shipyards. Geoff Searle, BAE Systems’ programme director for the Global Combat Ship, says a pilot capability was implemented in January and has now been rolled out to other sites across the UK.
"By wearing 3D glasses and headsets [the engineers] can stand in a full-scale 3D virtual compartment of the ship and use that to get a much better awareness of the full-size layout of the ship, spatial orientation and the optimum positioning of equipment and systems," Searle said at a recent briefing on the Type 26.
He added: "We’ve been working very closely with the RN [Royal Navy] operators and our engineers to make sure we’re laying out the ship in the most effective way possible."
Working with external suppliers, the Royal Navy and other BAE Systems’ offices across the UK, the company has already finalised many of the design details for the Type 26. This is despite the UK government still not having placed a firm order. An order for 13 ships is expected to be placed soon after the 2015 general election and when it is, BAE will be ready to begin the manufacturing process in earnest, owing to the detailed design work already being completed.
Virtual reality and building highly-complex nuclear subs
It’s not the first time BAE Systems has utilised innovative VR technology in the design process. For the Astute submarine programme – a project which involves the design and manufacture of seven highly complex nuclear submarines – the company did away with building expensive physical prototypes and instead, utilised shopfloor VR ‘pods’ made by Cheshire-based Virtalis.
"The VR models give you a very real sense of the boat from the inside. People can literally drop in and walk through the exact area they are building," said Dean Brown, Dimensional Control inspector at BAE Systems Submarine Solutions.
For the Astute programme, the VR pods are positioned close to the boats and are always accessible for individuals who are working on the project, whether it’s pipe fitters, welders or electricians. Visualisation tools are not just limited to CAD experts or IT professionals; it is about collaboration across different teams and different phases of the programme.
"If you think about somebody who’s invested an awful lot of time and money in coming up with a CAD model for a particularly complicated piece of machinery," explains Virtalis managing director David Cockburn-Price. "They can look at it on their desktop and they can get an idea of what it is like but imagine then being able to get up and get into a virtual prototype of that object. You can understand how the space works, how it feels to be in it as though it is really built."
For a truly immersive experience, engineers can even don an Oculus Rift-style head display and special VR gloves. Systems can track the motions of the user while they are inside a VR pod, meaning an engineer can look underneath objects by bending down or look around objects by moving their head left and right. With the aid of VR gloves, a user can pick up and manipulate components of a machine in a virtual environment.
"You really get inside that virtual world; you can see things at a 1:1 scale, you can understand them and interact with them, and that really makes you understand the data," said Cockburn-Price.
Companies such as Dassault Systèmes, a leader in PLM software for both defence and Formula 1, are finding ways to break down the traditional barriers between teams, partners, suppliers and customers to spur innovation in the full development cycle of a defence programme. Collaboration is being enhanced through new technologies like cloud computing, which allows for faster feedback and resolve times on designs. When time is money, it pays to have technology which can shave days and weeks off a process.
Innovation in armoured vehicles is taking place under the bonnet as much as elsewhere.
Collaboration is beneficial for large defence companies who have suppliers worldwide, aggressive time schedules and very complex systems to integrate. Advances in connectivity means engineers, suppliers and customers can often review designs, share comments and make alterations in real-time – similar to a Google Hangout – which was unheard of only a few years ago. Past programmes regularly used separate digital mock-ups across different sites, leading to extended design times and greater costs.
Design tools which can save lives, not just money
Siemens, another leading PLM software company, has also worked with BAE Systems’ Global Combat Systems (GCS) to help engineers and crews to develop enhanced capabilities and modifications for the British Army’s existing fleet of armoured vehicles and other equipment like naval guns and intelligent munitions. GCS uses a Siemens-developed virtual reality ‘dome’ which immerses engineers in a 360-degree environment and is used to assess life-size concepts with customers.
This type of technology has been particularly important for meeting urgent operational requirements over recent years, where rapid development has meant more than just saving money but also saving lives. "We used it on a number of military platforms and it has been hugely beneficial in identifying problems, integrating subsystems and selecting and agreeing on concepts at the design state," said David Vallis, manager of the Land Systems Integration Facility at BAE Systems GCS.
While huge warships and tanks may not have the sleek lines and beauty of a Formula 1 car, these days they share the same kind of precision design and engineering. Advanced design programmes, virtual reality and cloud computing are just a handful of new tools for today’s defence manufacturer. It is technology that will enable the British armed forces to remain in pole position for years to come.
Follow Grant Turnbull on Google+