The aerospace and defence industry continues to be a hotbed of innovation, with activity driven by the need to lower operational costs, larger consumer trends, and electrification, and growing importance of technologies such as hydrogen and electric aircraft and advanced materials. In the last three years alone, there have been over 174,000 patents filed and granted in the aerospace and defence industry, according to GlobalData’s report on Environment Sustainability in Aerospace, Defence & Security: Clean Ni-Co alloy extraction. Buy the report here.
However, not all innovations are equal and nor do they follow a constant upward trend. Instead, their evolution takes the form of an S-shaped curve that reflects their typical lifecycle from early emergence to accelerating adoption, before finally stabilising and reaching maturity.
Identifying where a particular innovation is on this journey, especially those that are in the emerging and accelerating stages, is essential for understanding their current level of adoption and the likely future trajectory and impact they will have.
180+ innovations will shape the aerospace and defence industry
According to GlobalData’s Technology Foresights, which plots the S-curve for the aerospace and defence industry using innovation intensity models built on over 262,000 patents, there are 180+ innovation areas that will shape the future of the industry.
Within the emerging innovation stage, hydrogen fuel cells, aircraft powertrain controls, and fuel cells for aircraft are disruptive technologies that are in the early stages of application and should be tracked closely. EV charging stations, hybrid propulsion aircraft engines, and electric aircraft charging interfaces are some of the accelerating innovation areas, where adoption has been steadily increasing. Among maturing innovation areas are fuselage frame modelling and powered wheels for aircraft landing, which are now well established in the industry.
Innovation S-curve for environmental sustainability in the aerospace and defence industry
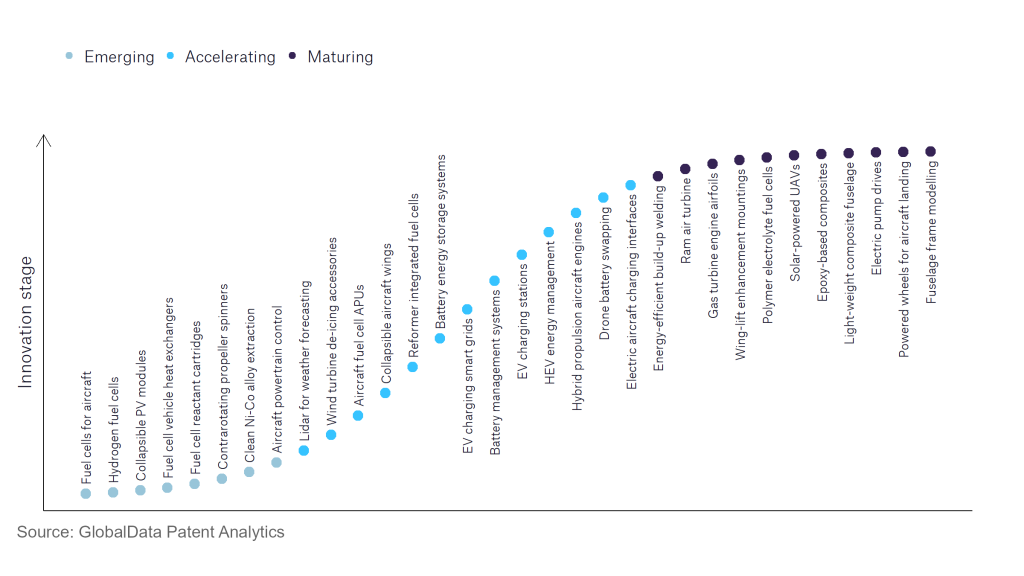
Clean Ni-Co alloy extraction is a key innovation area in environmental sustainability
Clean Ni-Co alloy extraction refers to the efficient extraction of Ni-Co alloys from superalloy scraps. The practice reduces wastage from valuable and energy intensive metal alloys.
GlobalData’s analysis also uncovers the companies at the forefront of each innovation area and assesses the potential reach and impact of their patenting activity across different applications and geographies. According to GlobalData, there are 10+ companies, spanning technology vendors, established aerospace and defence companies, and up-and-coming start-ups engaged in the development and application of clean Ni-Co alloy extraction.
Key players in clean Ni-Co alloy extraction – a disruptive innovation in the aerospace and defence industry
‘Application diversity’ measures the number of different applications identified for each relevant patent and broadly splits companies into either ‘niche’ or ‘diversified’ innovators.
‘Geographic reach’ refers to the number of different countries each relevant patent is registered in and reflects the breadth of geographic application intended, ranging from ‘global’ to ‘local’.
Patent volumes related to clean Ni-Co alloy extraction
Company | Total patents (2021 - 2023) | Premium intelligence on the world's largest companies |
General Electric | 40 | Unlock Company Profile |
Siemens | 33 | Unlock Company Profile |
CDP Equity | 24 | Unlock Company Profile |
Alstom | 19 | Unlock Company Profile |
Raytheon Technologies | 14 | Unlock Company Profile |
Rolls-Royce Holdings | 11 | Unlock Company Profile |
Mitsubishi Heavy Industries | 10 | Unlock Company Profile |
Hitachi | 10 | Unlock Company Profile |
Safran | 9 | Unlock Company Profile |
Porsche Automobil Holding | 6 | Unlock Company Profile |
EOS | 5 | Unlock Company Profile |
Source: GlobalData Patent Analytics
Amongst aerospace and defence companies, Raytheon Technologies is the leading patent filer in clean Ni-Co alloy extraction. In the aerospace and defence industry, these alloys are primarily used in jet engines, as well as in some electronic products. Raytheon Technologies is heavily involved in the production of aircraft engines through its subsidiaries, Collins Aerospace and Pratt & Whitney. The company produces a range of aircraft engines including the F135 installed on the F-35 Lightning II, the F117 installed on the Boeing C-17 Globemaster, and the Pratt & Whitney GTF engine. Other key patent filers include Rolls-Royce and Safran, both also leading aircraft engines producers.
In terms of application diversity, Raytheon Technologies holds the most widely applicable patents in clean Ni-Co alloy extraction, with Rolls-Royce and Safran coming in at second and third, respectively. Regrading geographic reach, Safran leads the way, followed by Raytheon Technologies and Rolls-Royce.
Clean Ni-Co alloy extraction is a promising avenue for aerospace and defence companies, specifically aircraft engine producers, to reduce waste and improve their sustainability performance. Increasing system efficiencies in production phases can reduce the carbon footprint of each product, allowing companies to enhance their ESG performance in a market which is increasingly being driven by environmental expectations and regulations.
To further understand the key themes and technologies disrupting the aerospace and defence industry, access GlobalData’s latest thematic research report on Defence.
Data Insights
From
The gold standard of business intelligence.
Blending expert knowledge with cutting-edge technology, GlobalData’s unrivalled proprietary data will enable you to decode what’s happening in your market. You can make better informed decisions and gain a future-proof advantage over your competitors.