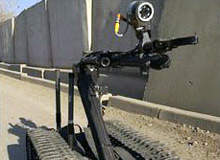
Since the dawn of mechanical transportation, humans have built their ground conveyances around the wheels-on-axles concept in order to convert energy into useful forward motion.
Now, however, the converging technological advances that are making robots autonomous and adaptable are beginning to influence fundamental design paradigms. Freed of the need to carry humans around, developers of unmanned ground vehicles (UGVs) are not only putting major new spins on the classic wheel-and-axle paradigms, but are even working on ways to replace the wheel altogether.
WHEELS AND TRACKS: ORANGES AND TANGERINES
All technologies embody tradeoffs, and to gain efficiency, the wheel sacrificed flexibility. Although optimal for roads and other flat, solid surfaces, wheels don’t do so well in off-road terrain.
To solve the off-road mobility problem in the age of mechanised power, innovators in the US and England came up with the tracked vehicle concept just over a century ago. But the precise analogue of the steel track is actually the rubber tire, and both devices derive power from axles that have limited ranges and dimensions of motion.
In either case, the locomotion principle is the same: the rubber (or steel) meets the road at the same place relative to the vehicle’s fixed chassis and centre of gravity.
How well do you really know your competitors?
Access the most comprehensive Company Profiles on the market, powered by GlobalData. Save hours of research. Gain competitive edge.
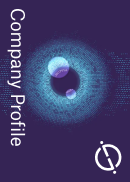
Thank you!
Your download email will arrive shortly
Not ready to buy yet? Download a free sample
We are confident about the unique quality of our Company Profiles. However, we want you to make the most beneficial decision for your business, so we offer a free sample that you can download by submitting the below form
By GlobalDataThe net result is that UGVs based on traditional vehicle designs essentially retain the same mobility constraints as manned vehicles. Conversely, creating UGV structures from a blank slate will ultimately enable UGVs to reach their full potential.
FUTURE LOCOMOTION: NEW MINDS IN NEW BODIES
UGV structural designs can be divided into three or four generations, akin to the ‘internet 1.0/2.0’ distinction that currently shapes thinking about future software. Notably, generational progress is proceeding along two related but separate dimensions: mechanical locomotive structure and electronic system control.
Generation 1.0 consists of remotely controlled vehicles that otherwise have traditional structures and capabilities, particularly in terms of locomotion. Notable examples include the driverless cars that have competed in DARPA’s Grand and Urban Challenges, as well as Foster Miller’s TALON robots, thousands of which currently perform bomb-disposal tasks in Iraq and Afghanistan.
This first wave of UGVs essentially puts a camera, mechanical control devices, and a radio in the driver’s seat, while leaving the rest of the vehicle unchanged. Consequently, this generation has two generic limitations: a need for constant attention and direction by human operators, and limited ability to negotiate difficult or previously inaccessible terrain.
Generation 2.0 comprises vehicles with enhanced motility built into their locomotive structures. A prime example is Lockheed Martin’s MULE (multifunction utility / logistics and equipment), which has two design innovations that enhance mobility in rough terrain.
Its six wheels are individually attached to separate articulated axles that can adjust wheel position in all three dimensions – a form of independent suspension that permits the robot to negotiate irregular discontinuous surfaces such as low walls. Should one of the wheels or axles be disabled, the robot can adjust its centre of gravity to drive on five (or even as few as three) wheels.
This second wave of UGVs represents significant but still evolutionary innovation in locomotive structure. Similarly, the UGV has enough intrinsic computer power to make adaptive adjustments to its basic functional processes, but the remote human driver still operates the vehicle.
A BREAK WITH TRADITION
Generation 3.0 features true revolutionary departures from the existing paradigms of axled locomotion and human command. The latter appears less futuristic, if only because UAVs already employ similar technologies, but is actually more impressive in that ground environments are much more cluttered and chaotic than midair environments.
A high-profile example of transferring decision-making responsibility from operator to robot is the Crusher UPI programme, managed by DARPA’s Tactical Technology Office (TTO). The UPI programme integrates the Spinner UGCV (a Gen 1.5 platform) with the PerceptOR (perception for off-road robotics) programme.
In turn, PerceptOR combines multimodal sensory technology such as machine vision and gyroscopes with more radically innovative autonomous navigation algorithms, which ideally would be able to perform ‘local path optimisation’ (intelligently deciding which obstacles can be avoided and which must be negotiated).
The more exotic side of Generation 3.0 is the incorporation of naturally occurring locomotion techniques into robotic technology. Biomimetics, the mimicry of biological design, treats evolution and natural selection as the ultimate proof-of-concept validators, and in the animal kingdom, the wheel is conspicuous by its absence.
EVOLUTIONARY DESIGN
Evolution has produced two alternatives for all-purpose ground locomotion – slithering and walking – and DARPA has research projects in both areas.
The TTO’s version of the snake is the multi dimensional mobility robot (MDMR) programme, which will investigate the use of ‘serpentine mobility’ concepts to navigate extreme terrain such as highly slippery surfaces and near-vertical slopes. Of course, the other critical capacity of a snake is that it’s narrow and flexible, and thus can wriggle into rock fissures, ventilation shafts, and other spaces that might be found in, say, sites like the Tora Bora complex in Afghanistan.
DARPA has several walking robot programmes. One such vehicle is TTO’s Big Dog, a four-legged ‘pack mule’ developed by Boston Dynamics. Big Dog has become a minor Youtube celebrity due to its ability to regain its footing after slipping on ice – without human intervention.
Similarly, the Strategic Technology Office (STO) manages the urban ops hopper programme, which aims to develop a hybrid legs-with-wheels robot with a vertical jump several times greater than that of your average pro basketball player.